Introduction
In the fast-paced manufacturing industry, optimizing work-in-process (WIP) management is critical to reducing production bottlenecks, minimizing errors, and ensuring timely delivery. RFID WIP tracking is becoming a key technology for manufacturers to achieve real-time visibility of production lines. By embedding RFID tags into raw materials, components, and parts, companies can automatically collect data, enhance traceability, and streamline workflows. This article explores how RFID technology is revolutionizing WIP manufacturing and solving common challenges in modern production environments.
What is WIP?
WIP (Work-in-Process) refers to partially completed goods that are still undergoing the production process. These items are no longer raw materials, but have not yet become finished products. Effective WIP management ensures that resources are allocated efficiently, reduces idle time, and prevents overproduction. However, traditional manual tracking methods often lead to inaccuracies and delays. This is where RFID WIP tracking comes in, providing an automated, precise, and scalable solution.
How RFID Technology Enhances WIP Manufacturing?
RFID (Radio Frequency Identification) uses electromagnetic fields to wirelessly identify and track tags attached to objects. Unlike barcodes, RFID does not require line-of-sight scanning, making it ideal for dynamic manufacturing environments. Here’s how it works:
- RFID tags: Small, durable chips embedded in WIP items, pallets, or containers.
- Readers and antennas: Installed at key checkpoints (e.g., assembly stations, quality control areas) to capture tag data.
- Software integration: Data is synchronized with the Manufacturing Execution System (MES) or ERP platform for real-time analysis.
Key Applications of RFID in WIP Tracking
1.Real-time Visibility Across Production Lines
RFID tags enable manufacturers to monitor the exact location and status of WIP items as they move through stages such as processing, assembly, and testing. For example, automotive manufacturers use UHF RFID to track engine parts, ensuring that each part meets quality standards before entering production.
2.Automated Inventory Management
By scanning WIP batches with RFID tags, companies can automatically update inventory levels and reduce manual counting errors. This is especially valuable in high-mix, low-volume production with high SKU complexity.
3.Quality Control and Traceability
RFID tags store historical data such as production dates, machine settings, and inspection results. If a defect is detected, manufacturers can trace back to the source of the problem, minimizing recalls and waste.
4.Reduce downtime with predictive analytics
An integrated RFID system analyzes WIP flow patterns to identify bottlenecks (e.g., machine stalls or shipment delays). Proactive adjustments ensure production stays on schedule.
5.Compliance and Audit Readiness
Industries such as aerospace and pharmaceuticals require strict compliance documentation. RFID-generated logs provide an auditable record of WIP processing, ensuring compliance with regulatory standards.
Why leading manufacturers adopt RFID for WIP tracking?
- Accuracy: Eliminate human errors in data entry.
- Speed: Scan hundreds of tags simultaneously, even in harsh environments.
- Scalability: Adjust the system for small workshops or large factories.
- Cost efficiency: Reduce labor costs associated with manual tracking.
Implementing RFID WIP Tracking:
Industry Pain Points: Inaccurate inventory or delayed shipments, etc.
Choose the right RFID tags: Select rugged, high-temperature tags for industrial environments.
Integrate with existing systems: Ensure RFID data flows seamlessly into MES/ERP platforms.
Pilot testing: Start with one production line and refine workflows before full rollout.
Case Study: RFID in Automotive WIP Management
A leading automotive supplier implemented UHF RFID tags to track transmission components across 12 assembly stations. Results include:
- A 30% reduction in manual data entry time.
- 99.8% inventory count accuracy.
- 20% faster defect resolution through enhanced traceability.
Conclusion
RFID WIP tracking is no longer a futuristic concept—it’s a practical solution reshaping modern manufacturing. By leveraging RFID tags to automate data collection and enhance visibility, businesses can optimize production efficiency, reduce costs, and maintain competitive agility. As industries continue to embrace Industry 4.0, RFID stands out as a vital tool for smarter, more responsive WIP manufacturing.
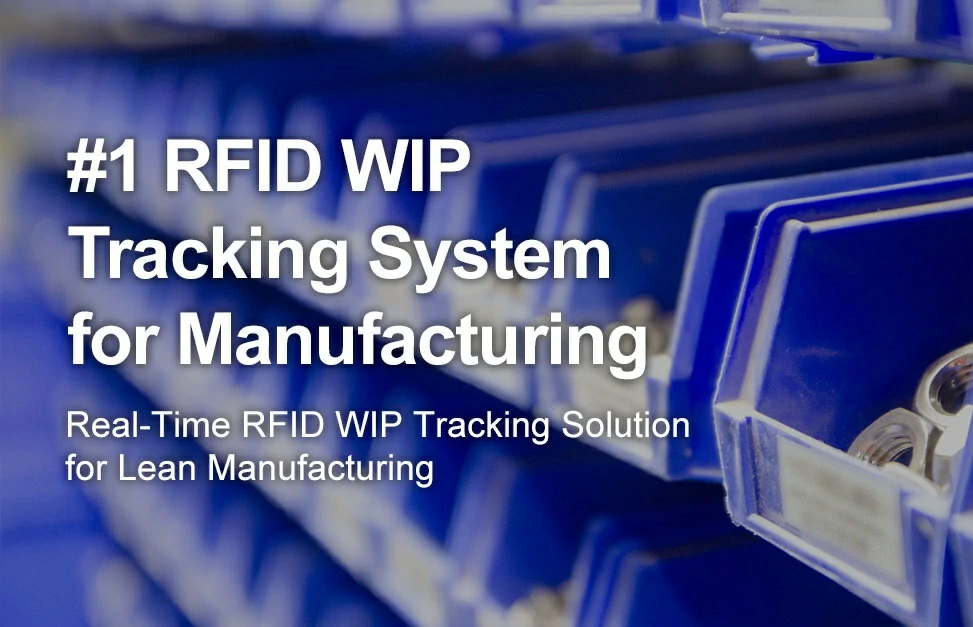